Sun Yat-sen University Thesis Project: Under the guidance of Prof. Deshan Meng, I explored the design of a lever arm amplification joint mechanism for tendon-driven robotic systems. This undergraduate thesis project focused on improving torque output capabilities while maintaining a lightweight design.
Project Overview
Institution: Sun Yat-sen University, ShenZhen, CN
Advisor: Prof. Deshan Meng
Duration: December 2023 - May 2024
Research Type: Undergraduate Thesis Project
This undergraduate research project investigated the design and implementation of a novel joint mechanism for tendon-driven robotic systems. The focus was on developing a lightweight joint design that could achieve improved torque output through lever arm amplification principles.
Research Background and Problem Statement
Tendon-driven robotic systems offer advantages in terms of lightweight design and remote actuation capabilities. However, achieving high torque output while maintaining system compactness remains a challenge. This research explored a potential solution through the design of a lever arm amplification joint mechanism.
The project aimed to address the following key challenges:
- Designing a compact joint mechanism that can effectively amplify output torque
- Maintaining lightweight characteristics while ensuring structural stability
- Developing a practical prototype for experimental validation
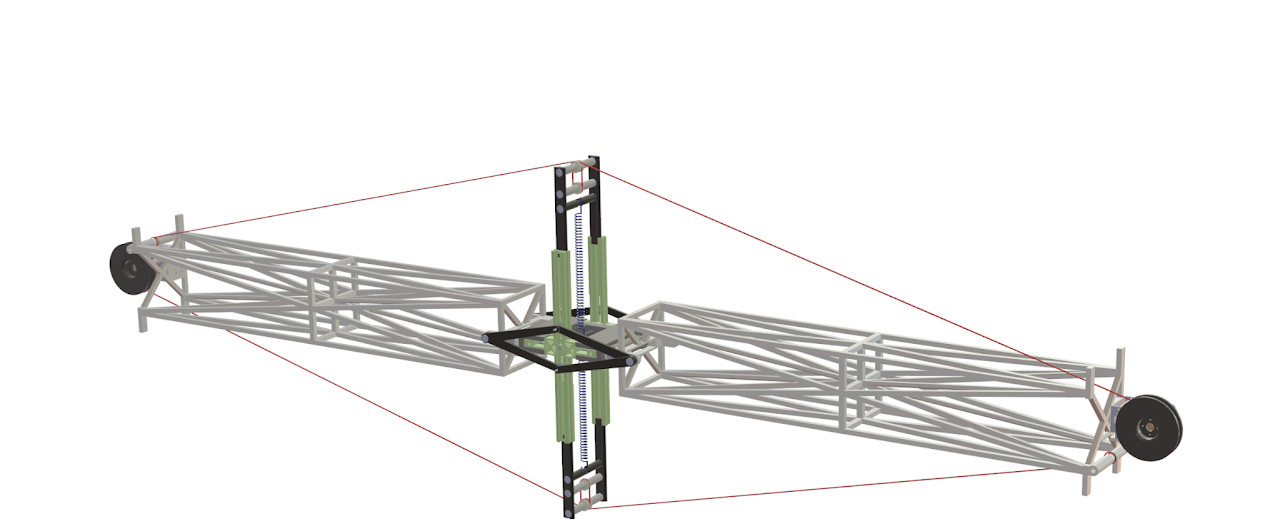
Technical Approach: Lever Arm Amplification Joint
The core focus of this undergraduate thesis was the development of a lever arm amplification joint mechanism. The design aimed to enhance torque output capabilities in tendon-driven systems through mechanical advantage principles, while maintaining a compact and lightweight structure.
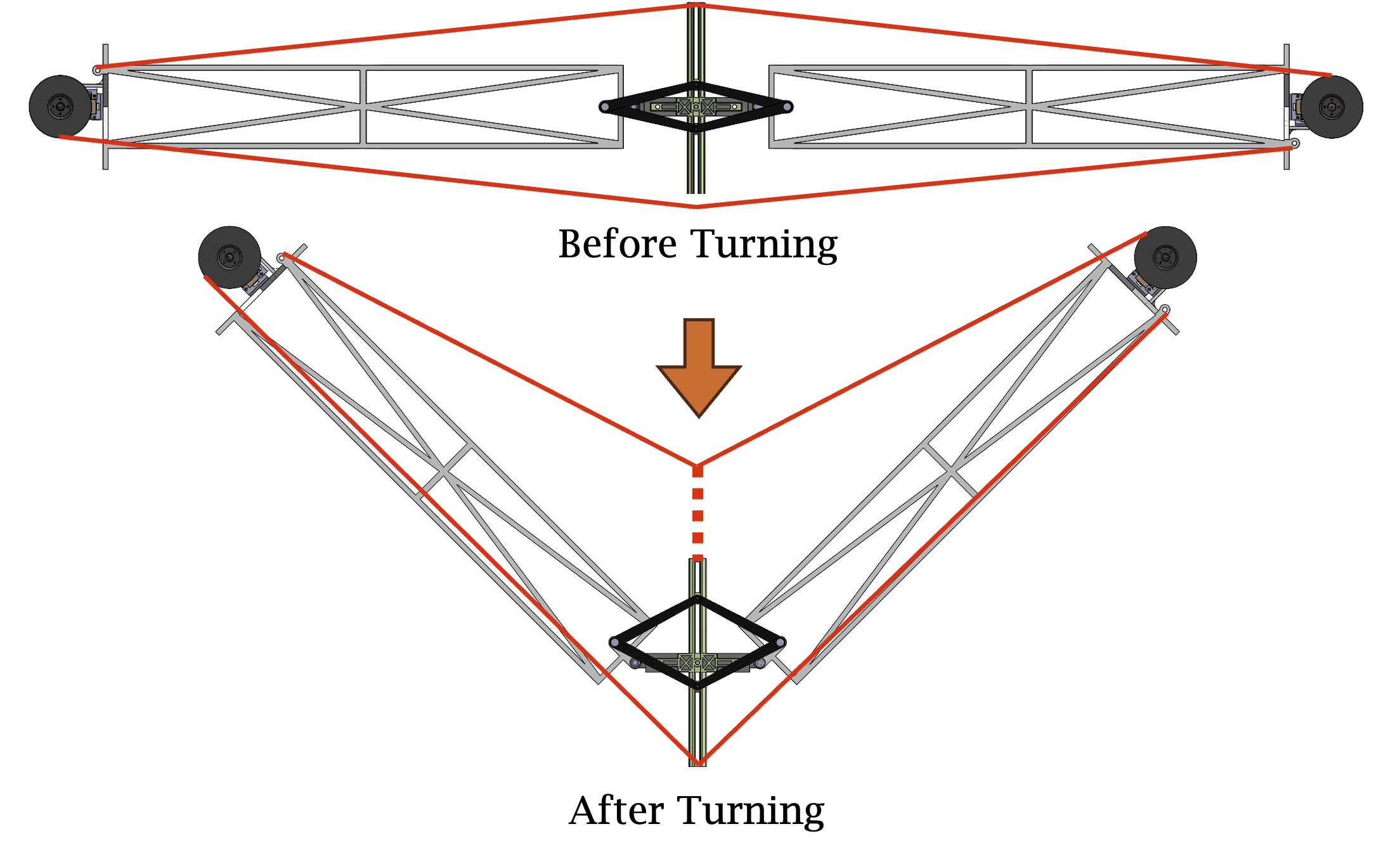
Development of a joint mechanism utilizing lever arm principles for torque amplification
Creation and testing of a functional prototype to validate the design concept
Evaluation of the joint mechanism's behavior under various operating conditions
Iterative refinement of the mechanism design based on test results
Research Methodology
The project followed a systematic approach combining theoretical analysis with practical implementation:
- Initial concept development and mechanical design of the lever arm mechanism
- Kinematic analysis to understand joint behavior and force transmission
- Prototype fabrication using appropriate materials and manufacturing techniques
- Experimental testing to validate the mechanism's performance
Prototype Development
A functional prototype was developed to validate the lever arm amplification concept. The prototype allowed for testing of the joint mechanism under various conditions and provided valuable insights for design optimization. Key aspects of the prototype development included:
- Component design and selection for the joint mechanism
- Assembly and integration of the mechanical systems
- Implementation of the tendon routing system
- Testing setup for performance evaluation
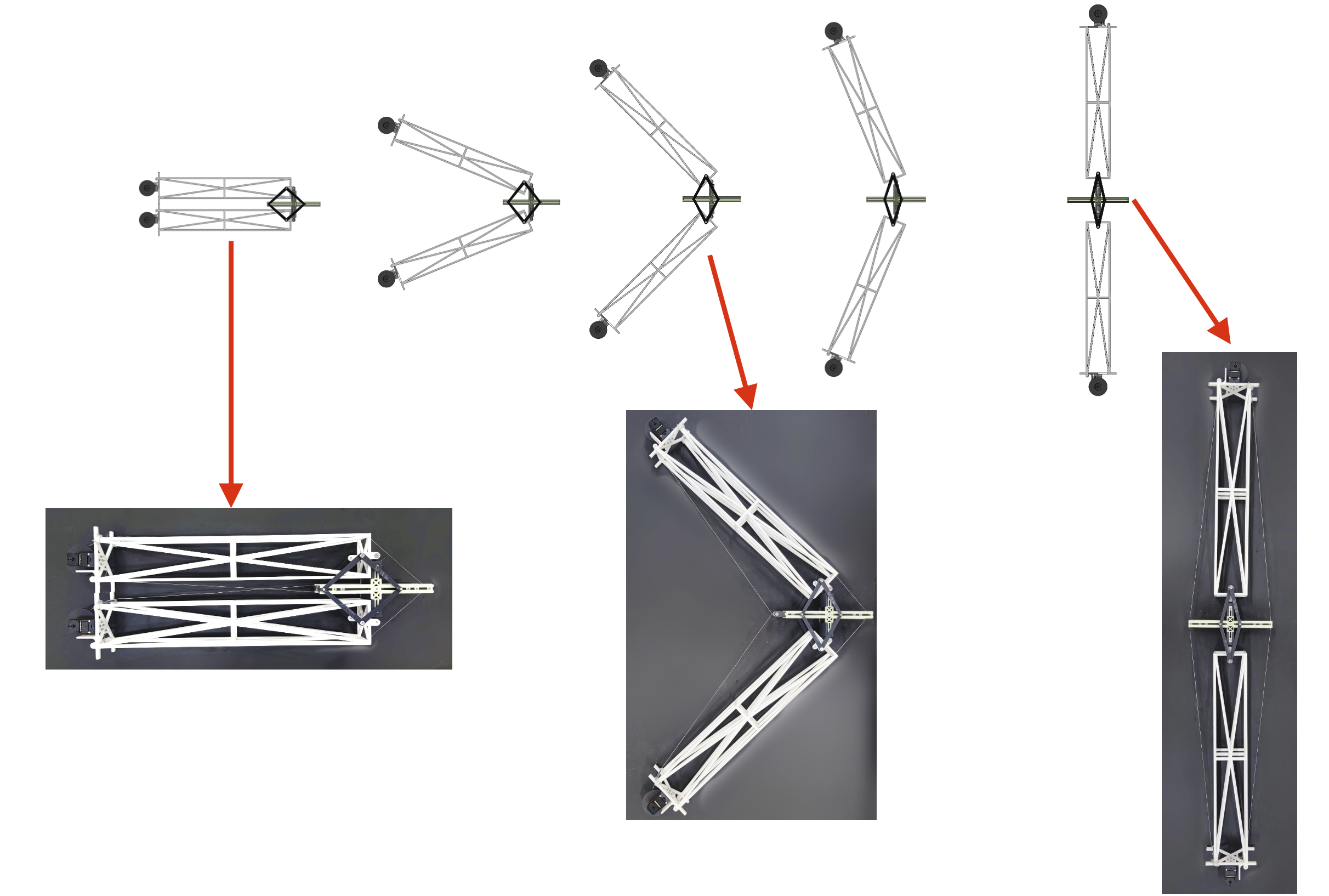
Research Results
The research successfully developed and tested a prototype of the lever arm amplification joint mechanism. The experimental results demonstrated the feasibility of the design concept for improving torque output in tendon-driven systems while maintaining lightweight characteristics.
Applications
While the research was conducted with space robotics applications in mind, the developed joint mechanism could potentially be adapted for various robotic applications where high torque output and lightweight design are important considerations.
Future Research Directions
This undergraduate thesis project laid groundwork for potential future research in tendon-driven robotic systems. Future work could explore:
- Advanced control algorithms for precise joint angle control
- Integration of multiple joints into a complete robotic arm system
- Further optimization of the lever arm mechanism for specific application requirements
- Experimental validation under various loading conditions
Conclusion
This undergraduate thesis project successfully explored the design and implementation of a lever arm amplification joint mechanism for tendon-driven robotic systems. The work combined theoretical analysis with practical prototyping, providing valuable hands-on experience in mechanical design and robotics research.
System Optimization and Future Research Directions
Through comprehensive system optimization of space-domain driven robotic arms, this research successfully achieved intelligent adjustment for cable-driven robotic arm systems. The optimization process focused on enhancing overall system performance while maintaining the core advantages of lightweight design and high torque output capabilities.
The success of this undergraduate thesis opens several avenues for future exploration. Advanced control algorithms, multi-joint systems, and integration with autonomous navigation could further enhance the capabilities of tendon-driven space robotics. Future research could explore adaptive control strategies that dynamically adjust lever arm configurations based on task requirements.
The principles developed in this research could also be applied to terrestrial robotics where high force-to-weight ratios are crucial, such as search and rescue operations, medical robotics, and industrial automation in weight-sensitive applications. The mathematical modeling framework and 3D manufacturing techniques developed could be extended to create more complex multi-degree-of-freedom systems.