Research Breakthrough: I participated in developing a stimuli-responsive flexible material inspired by the musculoskeletal system at Sun Yat-sen University. By applying Joule heating, we achieved real-time modulation of stiffness in the soft layer while maintaining compliant interaction capabilities. This work was published in Advanced Engineering Materials (JCR Q2, IF = 3.6).
Introduction
To enhance their versatility for diverse applications, soft machines often require stiffness-tuning strategies—for example, increasing structural stiffness to manipulate heavier objects. However, most existing programmable stiffness approaches struggle to maintain compliant interaction capabilities once structural rigidity is increased.
Addressing this challenge, researchers propose a stimuli-responsive flexible material inspired by the musculoskeletal system. The team demonstrates its application potential by developing three types of soft machines: a soft robotic gripper, a flexible wearable device, and a deployable structure for post-disaster rescue.
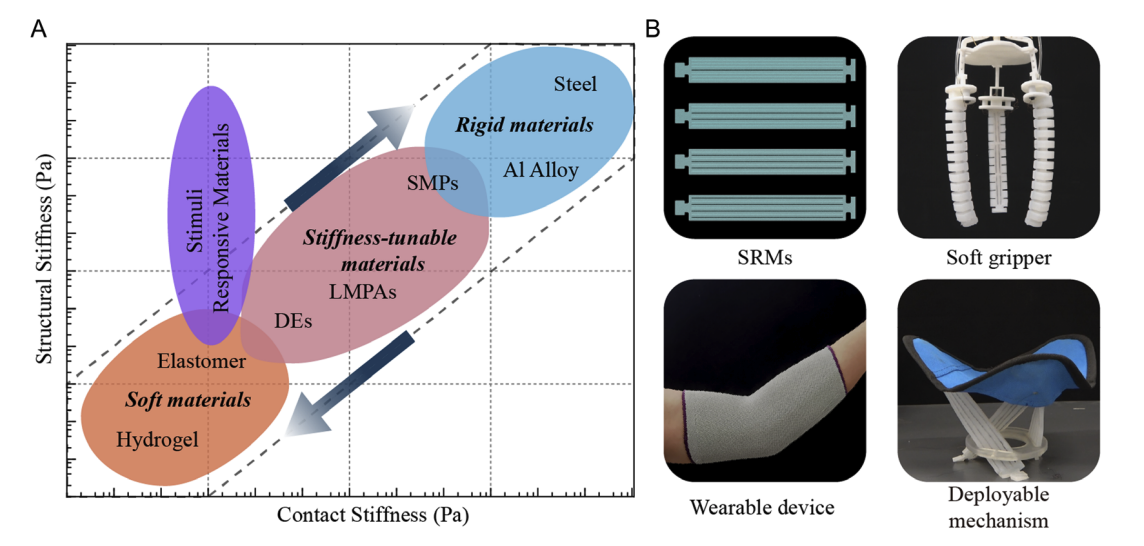
Bio-Inspired Design Philosophy
Biological systems reveal the complex interplay between structure and function, offering breakthrough ideas for the advancement of soft robotics. Muscle structures use chemical energy to produce various contraction responses and exhibit different stiffness levels between passive (minimal stiffness) and active (maximum stiffness) states, enabling stiffness modulation.
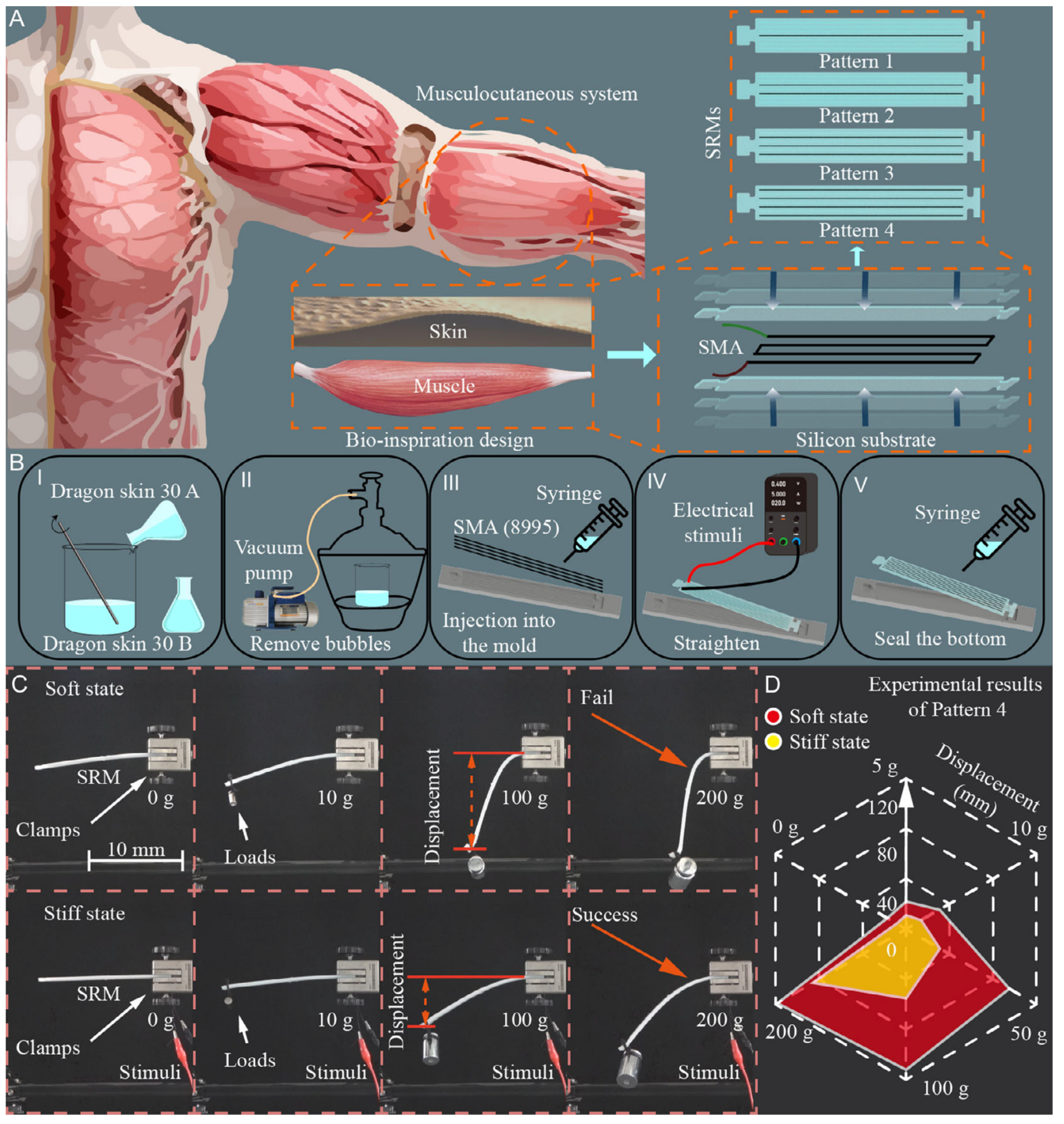
Meanwhile, the dermis—composed of collagen and elastic fibers—provides adaptive interaction capability. This biological paradigm inspired the development of an intelligent soft material (SRM) that integrates smart material components.
Material Architecture
The SRM design incorporates two key components:
- Shape Memory Alloy (SMA): Mimics muscle function for structural stiffness regulation
- Silicone Substrate: Simulates skin for maintaining compliant contact properties
Unlike conventional SMA-driven soft robots, the SRM exhibits bio-like stiffness enhancement under Joule heating, enabling real-time mechanical modulation. At the same time, the silicone base maintains low contact stiffness, preserving compliance in environmental interactions.
Performance Characteristics
To characterize the thermomechanical properties of this material, the team recorded temperature changes using infrared thermal imaging during actuation and conducted DSC (Differential Scanning Calorimetry) experiments on the SMA.
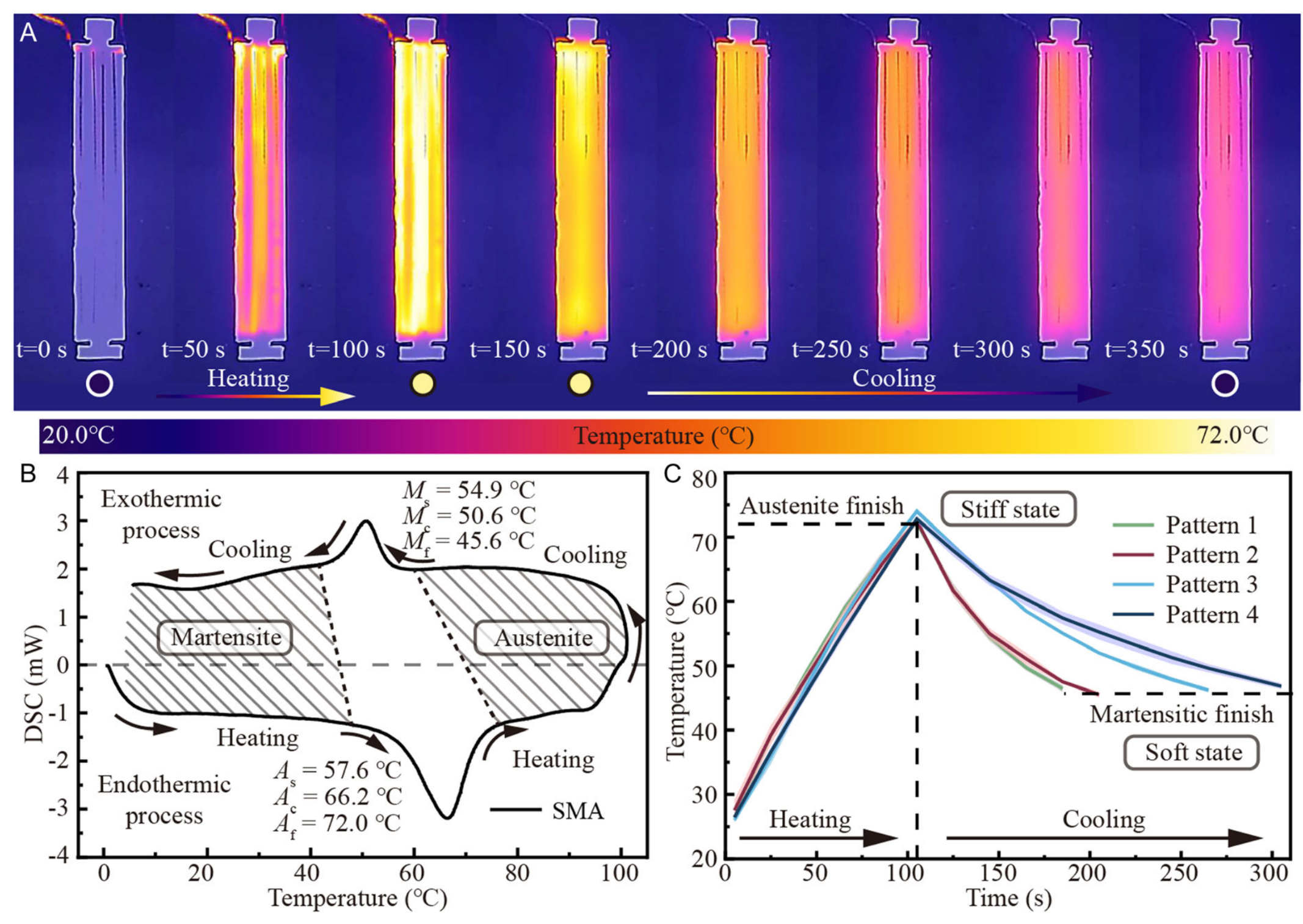
Stiffness Modulation Validation
To validate both the stiffness modulation and compliant contact capability of the SRM, the team performed three-point bending tests and surface contact stiffness measurements. Results demonstrated remarkable performance:
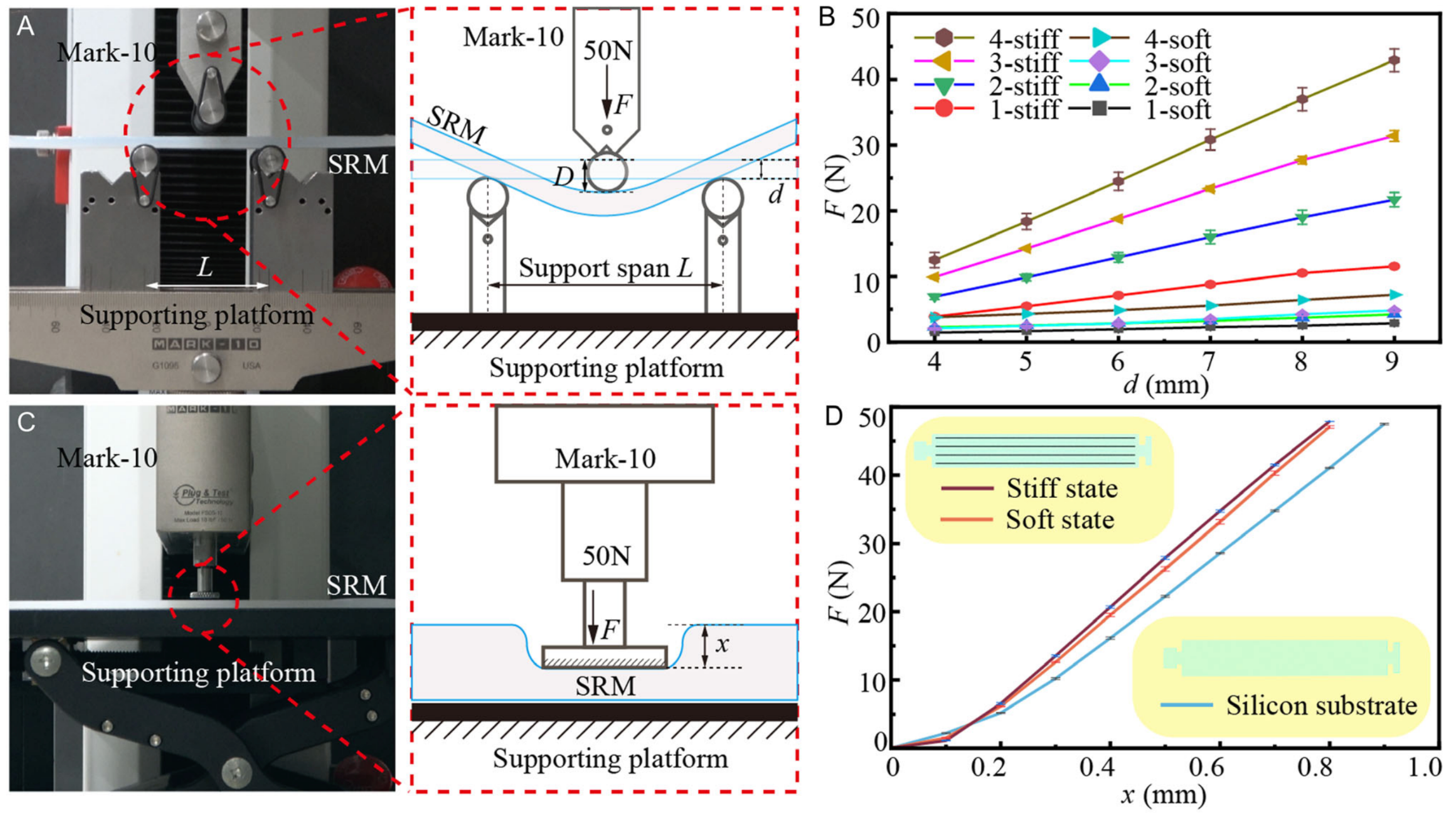
- Structural Stiffness: Bending modulus increased from 6.6 MPa to 142.4 MPa after activation
- Contact Compliance: Surface contact modulus remained around 2.2 MPa, comparable to plain silicone (1.95 MPa)
- Dual Functionality: Effective structural stiffness regulation while maintaining soft environmental contact
Applications and Impact
The research demonstrates the application potential through three distinct soft machine implementations:
1. Soft Robotic Gripper
Enhanced grasping capabilities for objects of varying weights while maintaining gentle contact with delicate items.
2. Flexible Wearable Device
Adaptive stiffness for ergonomic support while preserving comfort during human interaction.
3. Deployable Rescue Structure
Post-disaster applications requiring both structural integrity and safe human contact.
Innovation Significance: This research addresses a fundamental challenge in soft robotics by achieving simultaneous structural stiffness regulation and compliant contact maintenance—previously considered mutually exclusive properties.
Future Directions
The successful development of bio-inspired stimuli-responsive materials opens new avenues for:
- Advanced soft robotic systems with adaptive mechanical properties
- Smart wearable technologies with dynamic stiffness control
- Emergency response equipment with enhanced safety features
- Industrial automation systems requiring both strength and compliance
This breakthrough represents a significant step forward in creating truly adaptive soft machines that can respond intelligently to their environment while maintaining the safety and compliance characteristics that make soft robotics so promising for human-robot interaction applications.