Research Achievement: This research introduces a Hybrid Multimodal Gripper (HMG) that revolutionizes robotic grasping by combining pinch-suction mechanisms with soft-rigid coupling. Published in IEEE Transactions on Robotics (IF = 9.4), this work demonstrates unprecedented grasping diversity from 0.2g feathers to 10kg dumbbells.
Introduction
Universal grasping — the ability to adapt to a wide range of objects and tasks without requiring customized adjustments — is essential for robotic grippers. A key to achieving this lies in designing grippers with flexibility and adaptability, allowing robots to handle unknown objects and complex environments as humans do. However, the vast diversity in object weight, fragility, size, and shape poses long-standing challenges to this goal.
Previous studies have primarily adopted two strategies to enhance grasping diversity in robotic grippers: multi-mechanism fusion and soft–rigid structural coupling. However, current robotic grippers often suffer from conflicts between different mechanisms or structural elements, preventing full utilization of their advantages.
Multi-Mechanism Fusion
Each grasping mechanism has its limitations. For instance, enveloping grippers struggle with flat objects, while suction-based grippers cannot handle porous items. Combining pinch and suction mechanisms — inspired by an elephant trunk — significantly improves adaptability.
Soft–rigid structural coupling mimics the human finger's internal bone structure and outer soft tissue (muscles and skin), offering both strength and compliance. Rigid grippers provide high output force and precision but lack adaptability, while soft grippers are highly adaptive but have limited load capacity.
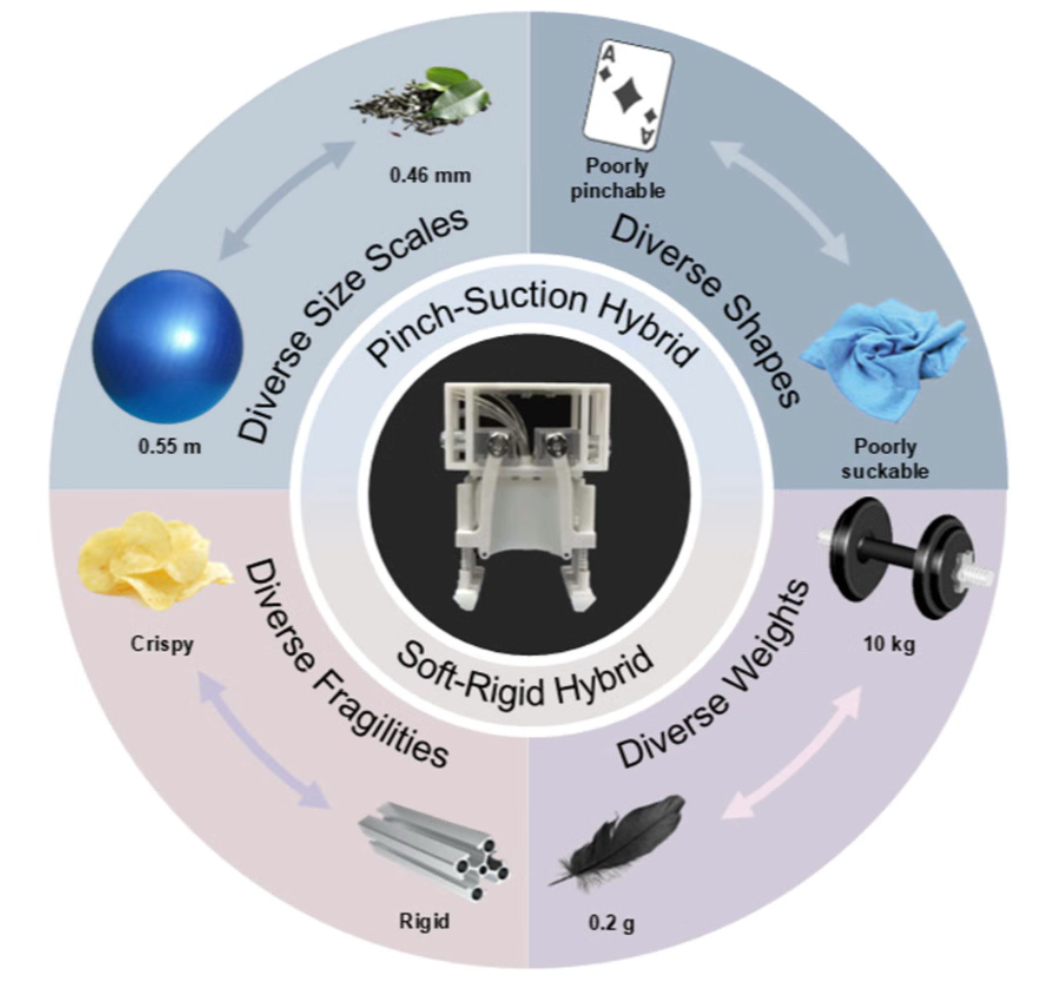
Multimodal Operation Design
The gripper features separate soft and rigid actuation systems, enabling four distinct operating modes through independent or combined control:
High-force grasping for heavy objects
Delicate handling of fragile items
Handling large or flat objects
Combined pinch + suction for stability
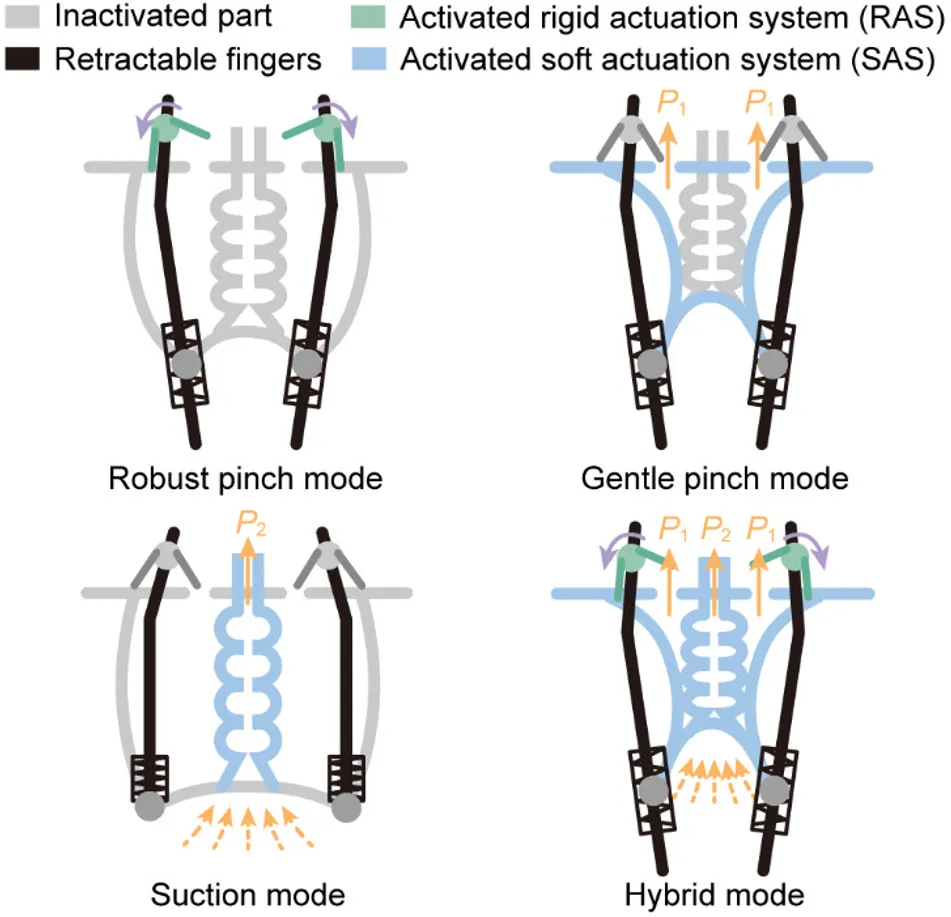
Selective Activation Mechanism (SAM)
The gripper incorporates a Selective Activation Mechanism (SAM), enabling complete decoupling between rigid and soft actuators to harness their respective advantages. Additionally, a compliant adaptive module — composed of passive telescopic fingers and a retractable soft suction cup — allows seamless switching between pinch and suction modes without additional actuators or active control.
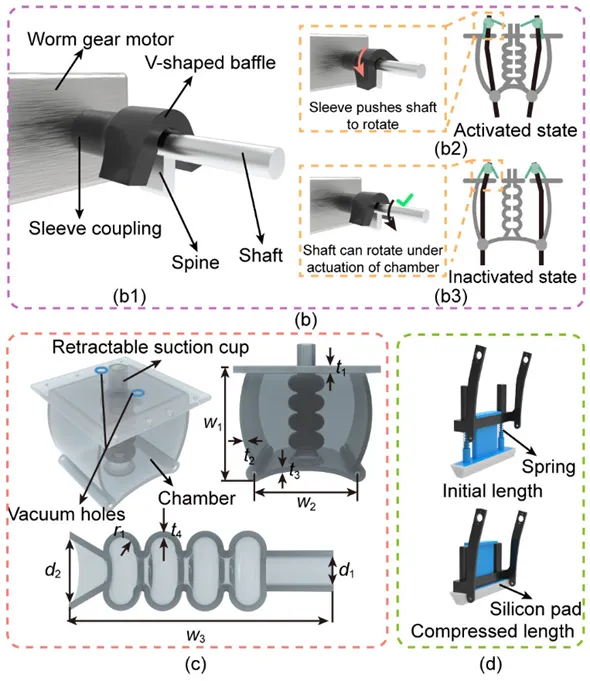
Exceptional Grasping Diversity
The soft structure allows gentle interaction with fragile items, while the rigid structure supports heavy, hard objects. The HMG demonstrates unprecedented versatility across multiple dimensions:
From 0.2g feather to 10kg dumbbell
From crispy chips to rigid aluminum
From 0.46mm tea leaves to 0.55m yoga balls
Flat cards, prickly cacti, porous towels
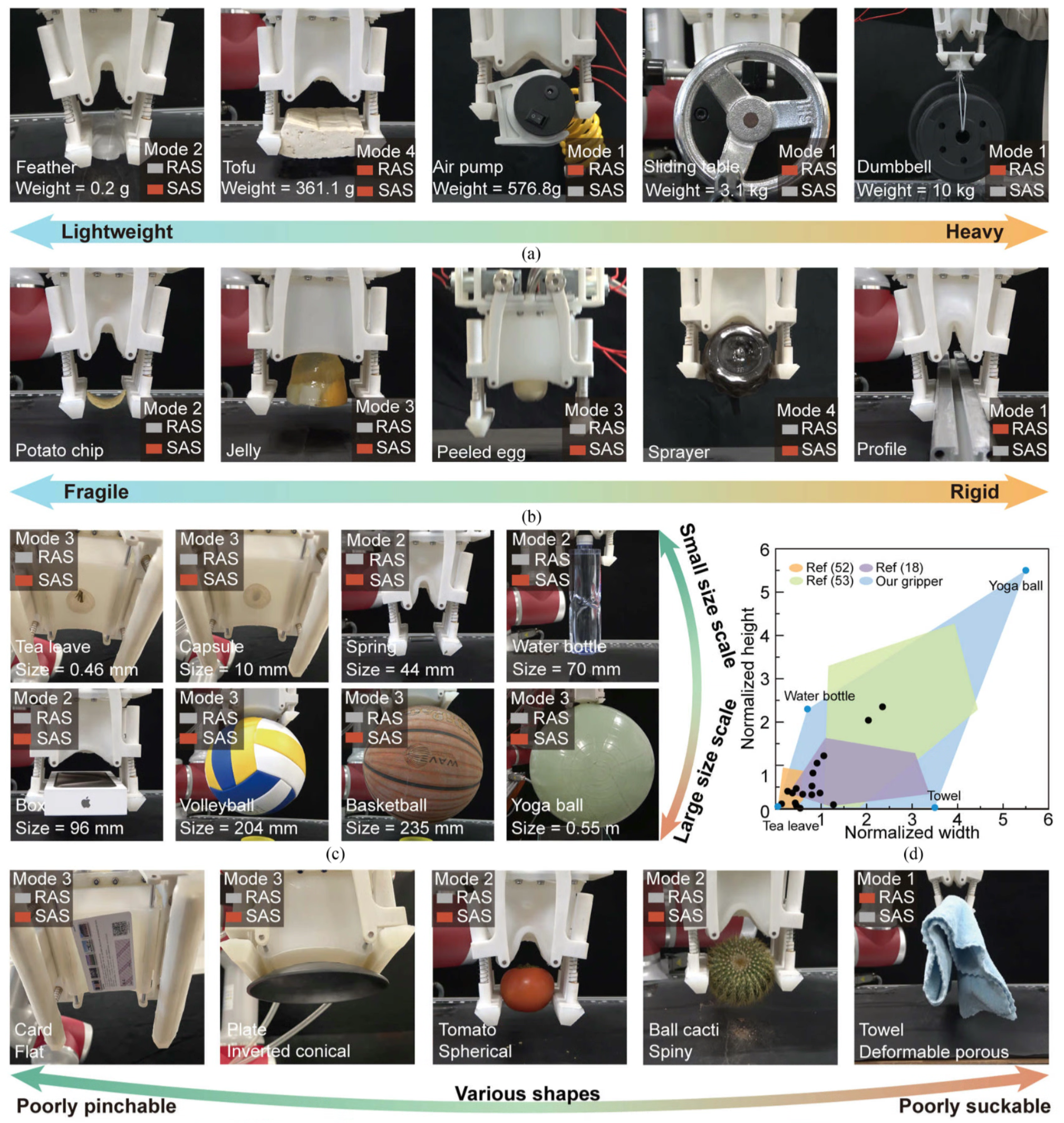
Advanced Capabilities
Dynamic Environment Performance
In dynamic environments (4.5 m/s² acceleration), HMG can robustly grasp irregular objects (e.g., plush toys, phone stands, model landscapes) in various orientations, demonstrating strong robustness and adaptability.
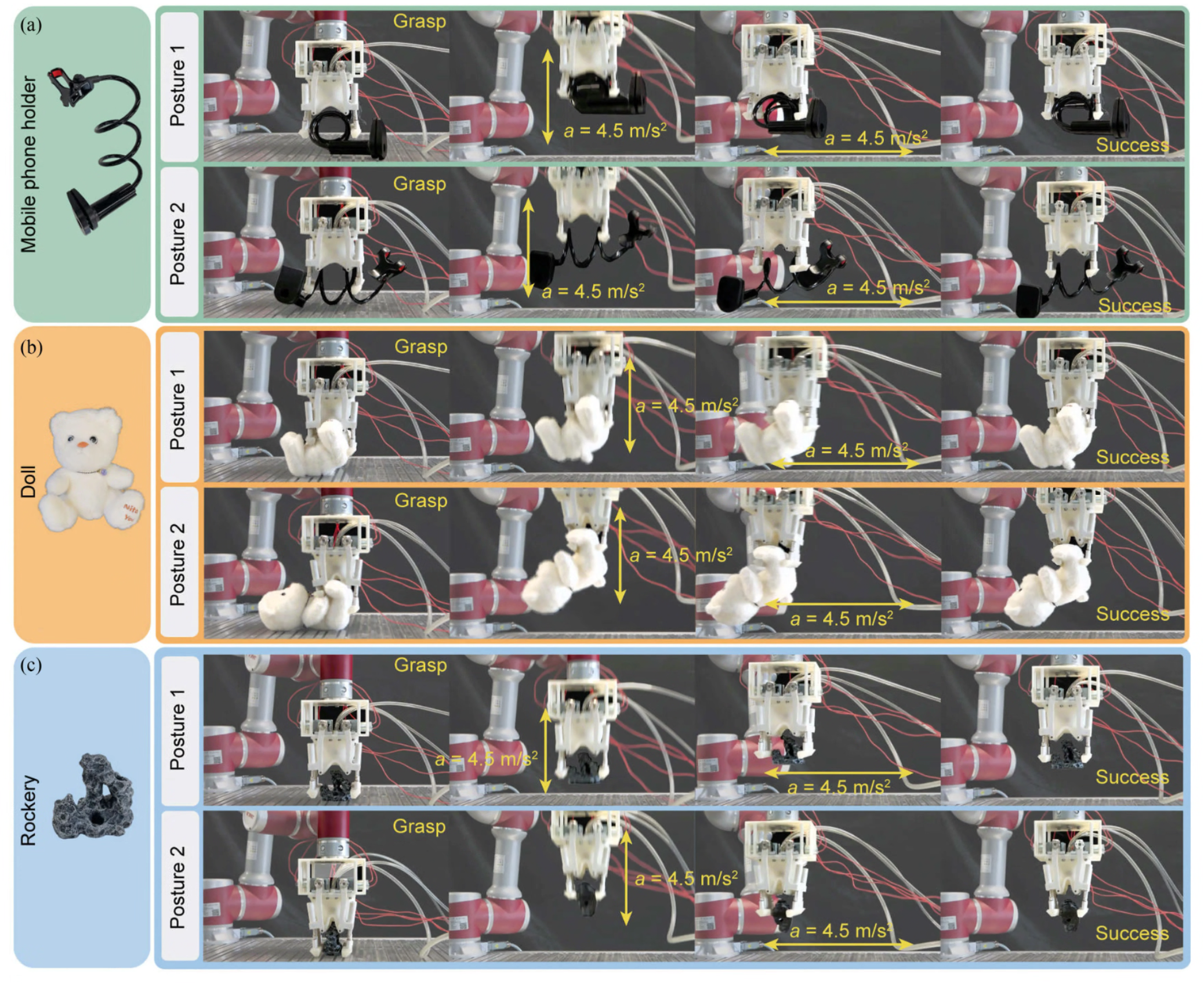
Closed-Loop Sensing
By integrating flexible pressure sensors at the fingertips and suction inlet, HMG gains perceptive ability during interactions, enabling closed-loop control for precise grasping according to preset instructions.
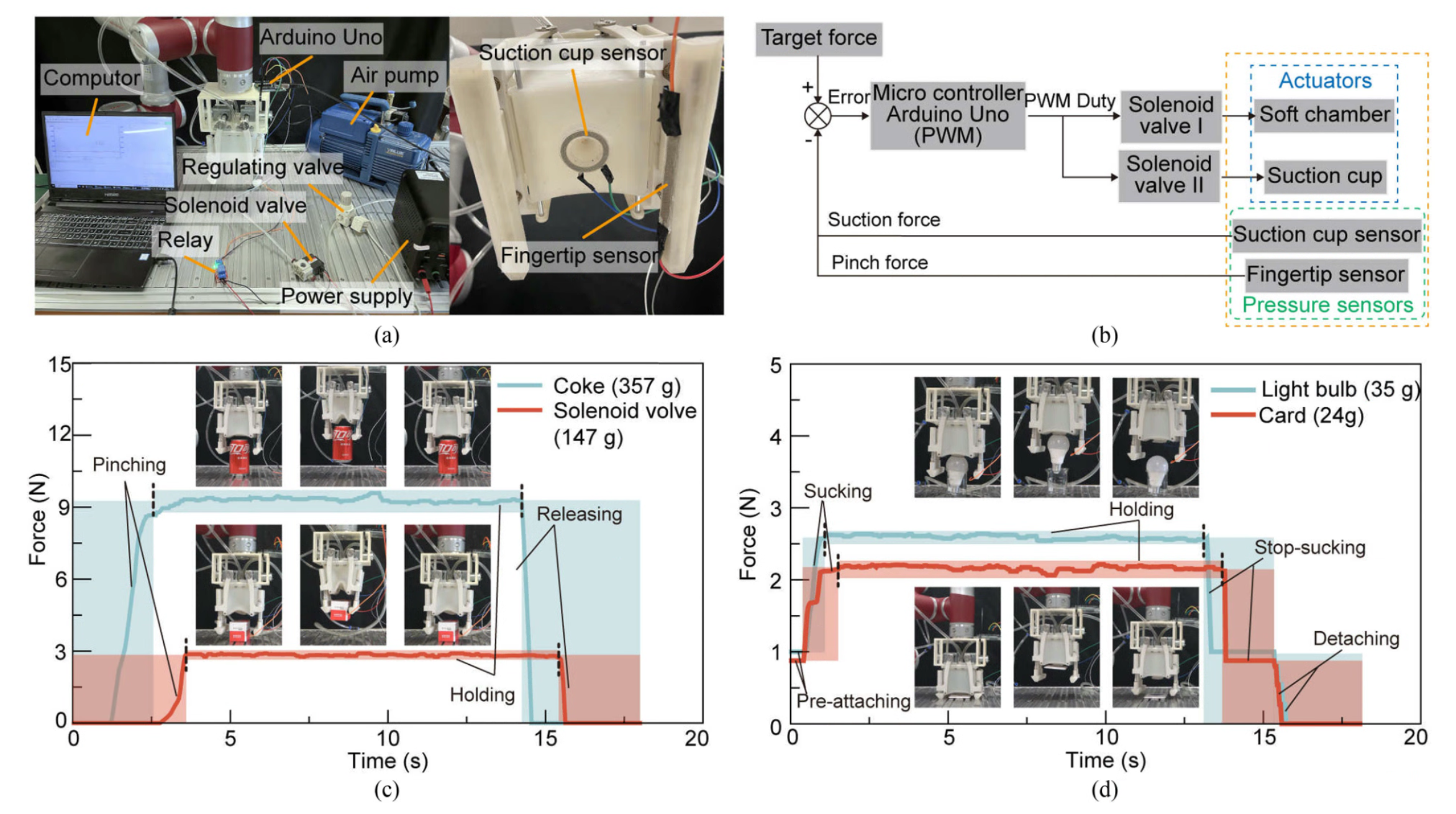
Real-World Applications
HMG excels in complex real-world tasks through coordinated multimodal operation:
- Industrial Applications: Assembly line operations, fruit-sorting pipelines
- Daily Life Tasks: Sorting books, pouring milk, cooking soup
- Underwater Operations: Sediment sampling, marine archaeology, debris collection
- Emergency Response: Rescue operations requiring gentle yet secure grasping
Innovation Impact: By integrating multiple grasping mechanisms and a soft–rigid coupled structure into one gripper, this research demonstrates — for the first time — the enormous potential for expanding grasping diversity and offers a simple yet effective design solution for multimodal coordination.
Future Directions
These capabilities highlight HMG's potential across daily life, industrial production, and specialized applications. The principles and mechanisms developed provide valuable references for the future development of high-performance robotic grippers, paving the way for truly universal grasping systems.
Future research directions include scaling the technology for larger industrial applications, improving sensing capabilities for better environmental awareness, and developing machine learning algorithms for adaptive grasping strategy selection.